Introduction
SCARA stands for selective compliant assembly robot arm or selective compliant articulated robot arm. It is a device which was designed to curb the problems of rotational and translational errors. It is a form of automation mostly applied in assembly jobs. It is designed in a way that it can perform the works which are performed by human beings. Human beings can cause errors especially where repetition is necessary. It can perform very high speed work effectively and at a very low cost. The SCARA robot is made in a way that its movements are smooth. The combination of rigid frame and rotation movements makes it comply with the horizontal in the horizontal plane. This combination is essential in assembly works. It is the mostly used kind of robot especially due to the new developments of heavier payload capacity, better intelligence integration and increasing variety of end effectors. 4-axis SCARA can perform a standard cycle in 29 seconds and within 20 microns of repeatability (Janine, 2005). EPSON’s SCARA robot has shown improvements in speed, repeatability and durability (Janine, 2005). Adept cobra has i600 SCARA robot which can perform high speed jobs and precise jobs. It can be used for mechanical assembly, material handling, packaging, machine tending, screw driving and screw driving plus any other application which needs fast and precise automation. It has proved to have a high level of efficiency.
Discussion
SCARA is the initials for selective compliant assembly robot arm or selective compliant articulated robot arm. It is the almost the oldest of all robots since it was developed in 1981 by Sankyo Seiki manufacturing company (Roland, 2011). It is one of the mostly used robots for assembly. It is mainly used for assembly and mimics the work that is done by human personnel (Roland, 2011). SCARA robot is mostly used since it works at very high speed, it’s efficient and it works at a low cost. It can be used to do a wide range of work even where repetition is required. It can be set in a way to handle a very precise installation. It also has another advantage that it has waterproof joints therefore it can be used for underwater construction (Roland, 2011). SCARA can also be controlled by remote therefore it can be used in places which are hazardous to human beings. For instance work site with poisonous emissions and harsh environmental conditions. SCARA robots are very important development in technology used for assembly because they have a wide range of motion, speed and precision (Roland, 2011). It works much faster than human beings can work. Because of efficiency, it increases production and lowers costs.
SCARA robot is composed of a linear vertical axis, two rotary axes to move the two arm linkages in the horizontal plane and an axis for wrist rotation. The vertical axis makes the vertical movements smoother and faster. It also has a very rigid frame which together with rotation motions ensures compliance in the horizontal plane. This is a very crucial combination in assembly jobs. It is mostly used by many companies because of its high repeatability of less than 0.025, high speed of 2000 to 5000mm/s, limited working envelops of less than 1000mm and payloads which range from 10 to 100kgs. It was initially used for precise, high speed and light assembly. Recently it has been used for large jobs which require complex assembly.
SCARA robots are mainly used in the line of automation because they are very flexible. It was designed to overcome rotational and translational errors. It is very stiff to rotations hence prevent any rotational error from occurring (William, 1994). It is also less stiff to displacements in a horizontal plane hence it can accommodate translational errors more easily (William, 1994).
SCARA has been the best in performing a lot of activities which consist of point to point movements. Some of these activities include dispensing, loading, pick and place, assembling and palletizing (Janine, 2005). Its use is being expanded especially due to the recent development which involves heavier payload capacity, better intelligence integration and increasing variety of end effectors. 4-axis SCARA can perform a standard cycle in 29 seconds and within 20 microns of repeatability (Janine, 2005).
There are the EPSON’s SCARA robot which is of two types; BN and BL. BN is a little bit smaller and is mostly utilized in applications which require less reach (Janine, 2005). BL is larger and is mostly utilized in greater payloads (Janine, 2005). The EPSON design is in such a way that it reduces the arm weight hence improving speed, repeatability and durability (Janine, 2005).
SCARA has undergone several improvements lately which go ahead to improve the work it performs. The most recent SCARA robot has improved intelligent integration, streamlined parts count and features like heavier payload capacity, simpler cabling and smaller space requirements (Janine, 2005). For instance the PowerScara helps in saving around 85% of the space which could be occupied by an ordinary SCARA. It is also easier to install it since it requires less cabling (Janine, 2005). It has maintenance free absolute encoders with two electronic evaluators (Janine, 2005). There are SCARA robots available via Staubli. These include; Turboscara SR4plus, SR6plus and SR8plus. Turboscara robots move in four axes making the operations easy and safe (Janine, 2005). They are more appropriate in activities which require high speed assembly like in electronics, automotive and food since they have the ability to achieve a high speed of up to 1600mm per second (Janine, 2005).
The Adept Cobra s600 SCARA robot can handle high performance jobs like conveyor tracking and vision guided motion. It also has around 70% reduced wiring, increased flexibility, scalability, and cost saving (Janine, 2005). The recent SCARA robots can handle much heavy payloads. For instance, the EPSON robot discussed earlier has handled the E2H853 heavy duty SCARA which had 20kg maximum payload and 0.45 kgm2 moment of inertia (Janine, 2005). In its accompaniment, E2H853 has user friendly EPSON RC+ software and powerful RC420 controller (Janine, 2005).
Since lighter and precise jobs still have to be done, SCARA robots are still being improved to perform these kinds of jobs. For instance, Yamaha supplies the smallest SCARA robots which can perform these light jobs. Especially due to repeatability 0.005 mm these small microbes can perform subminiature and high precision applications (Janine, 2005). They are available with arm lengths of 120 and 150 mm accompanied with a maximum payload of 0.5 (Janine, 2005).
Adept cobra has i600 SCARA robot which can perform high speed jobs and precise jobs. It can be used for mechanical assembly, material handling, packaging, machine tending, screw driving and screw driving plus any other application which needs fast and precise automation. It has proved to have a high level of efficiency. Adept’s SCARA robot continue especially by the introduction of the cobra i-series, s-series and PLC-series of SCARA robots. The i-series which consists of i600 and i800 have electronics which is attached to the robot arm (Direct Industry, 2011). The s-series consists of consists of s600 and s800 which are advantageous since they use the application capabilities made available by the external Smart Controller CX. Adept has the latest models which include cobra s350 and cobra s350 CR/ESD SCARE robots. These two are used to give cobra SCARA robot speed and performance mostly in a smaller motion envelop. SCARA Series Robots include; (Direct Industry, 2011) Adept Cobra s350, Adept Cobra s350 CR/ESD, Adept Cobra i600, Adept Cobra i800, Adept Cobra PLC600, Adept Cobra PLC800, Adept Cobra s600, Adept Cobra s800, Adept Cobra s800, Inverted, AdeptOne, ValueLine, AdeptOne-XL ValueLine, and AdeptThree-XL ValueLine.
EPSON still has another kind of a SCARA robot called E2C251S which has repeatability of 8 microns. It serves applications which do not require large robots. They can be perfectly used in fiber optics component assembly, hard disk assembly, and semiconductor die handling.
Conclusion
From the discussion, it can be concluded that SCARA robot is one of the most used robot in many assembly organizations. This is because it can reduce both rotational and translational errors, while at the same time it helps in increasing productivity and reducing costs. They can perform high speed jobs and smaller jobs, both which they perform with a high level of efficiency. Yamaha supplies the smallest SCARA robots which can perform these light jobs. Especially due to repeatability 0.005 mm these small microbes can perform subminiature and high precision applications. They are available with arm lengths of 120 and 150 mm accompanied with a maximum payload of 0.5. The Adept Cobra s600 SCARA robot can handle high performance jobs like conveyor tracking and vision guided motion. It has come with many advantaging including making the installation process easy due to few cables and saving on space because of its size.
References
Direct Industry. (2011). Assembly SCARA Robot. Retrieved on April 4, 2011 from http://www.directindustry.com/prod/adept-technology/assembly-scara-robots-6076-410843.html
Janine, N. (2005). SCARA Robots: Still Speedy and Dependable. Retrieved on April 4, 2011 from http://www.allbusiness.com/public-administration/justice-public-order/434701-1.html
Roland, P. (2011). What Is a SCARA Robot? Retrieved on April 4, 2011 from http://www.wisegeek.com/what-is-a-scara-robot.htm
William, D. (1994). Manufacturing Systems: An Introduction to the Technologies. Netherlands, Kluwer Academic Publishers.
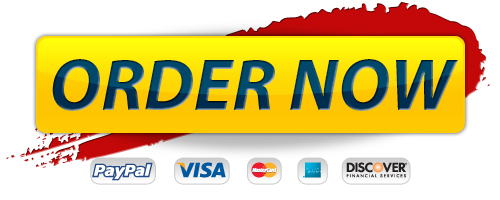
Order Management

Premium Service
- 100% Custom papers
- Any delivery date
- 100% Confidentiality
- 24/7 Customer support
- The finest writers & editors
- No hidden charges
- No resale promise
Format and Features
- Approx. 275 words / page
- All paper formats (APA, MLA, Harvard, Chicago/Turabian)
- Font: 12 point Arial/Times New Roman
- Double and single spacing
- FREE bibliography page
- FREE title page
0% Plagiarism
We take all due measures in order to avoid plagiarisms in papers. We have strict fines policy towards those writers who use plagiarisms and members of QAD make sure that papers are original.